So, What Exactly is a Thermoset Composite?
Thermosets are a class of materials that have become essential in a wide range of industries, from aerospace and automotive to electrical and consumer goods. These composites are known for their exceptional mechanical strength, thermal stability, and electrical insulating properties, making them ideal for demanding applications. But what exactly is a thermoset composite, and how do these materials attain these characteristics?
The history of thermosetting resins dates back to the early 20th century, with the invention of “Bakelite” by Leo Baekeland in 1907. Bakelite, the first synthetic plastic, was a phenolic resin that quickly found use in electrical insulators, radio and telephone casings, and various household items. This invention marked the beginning of the polymer revolution, leading to the development of other thermosetting resins like epoxy, melamine, and polyester. For this reason, it is a common misnomer to call the entire variety of thermosetting resins, “Bakelite”.
Over the decades, advancements in polymer chemistry and manufacturing techniques have expanded the applications of thermosetting resins. Today, these materials are integral to industries ranging from aerospace and automotive to construction and electronics.
What makes these materials ‘thermoset composites’?
A thermoset composite is a material composed of a thermosetting resin matrix reinforced with fibers or fillers. Unlike thermoplastics, which can be melted and reshaped multiple times, thermosetting resins undergo a chemical reaction when cured, forming a cross-linked, three-dimensional structure. Once cured, these materials cannot be re-melted or reshaped, giving them their characteristic rigidity and stability.
Popular Thermosetting Resins
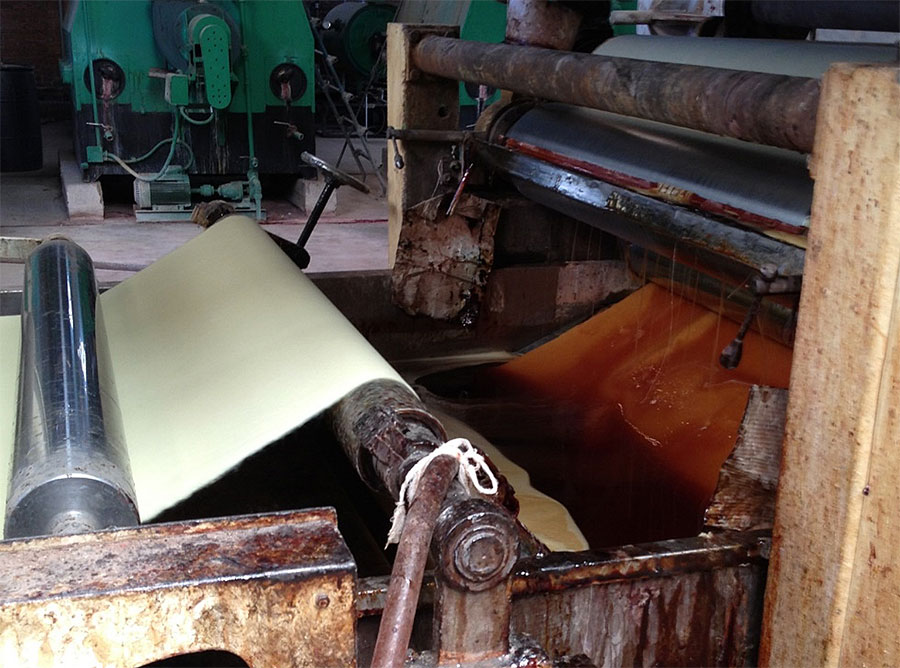
Phenolic Resins:
- History: As mentioned above, phenolic resins were the first synthetic polymers to be commercialized, developed by Leo Baekeland in 1907. The first commercial product, Bakelite, revolutionized the production of electrical insulators, household items, and automotive components.
- Properties: Phenolic resins are known for their excellent thermal stability, flame resistance, and low smoke generation. They are also chemically resistant and have good electrical insulating properties.
- Applications: Today, phenolic resins are widely used in electrical switchgear, circuit boards, and structural components in transportation and construction.
- Lamitex Phenolic Grades: XX, XXX, CE, LE, MF G, PF30, G3
Epoxy Resins:
- History: Epoxy resins were developed in the 1930s and became commercially available in the 1940s. They were initially used for coatings and adhesives, but their applications quickly expanded due to their versatility.
- Properties: Epoxy resins are known for their excellent mechanical strengths, thermal insulation (including cryogenic applications) chemical resistance, and strong adhesion to various substrates. They also exhibit exceptional electrical insulating properties.
- Applications: Epoxy resins are used in aerospace components, marine coatings, electrical laminates (e.g., Lamitex NEMA Grade G10, FR4, G11 & FR5), and high-performance adhesives.
Melamine Resins:
- History: Melamine resins were developed in the 1930s and were initially used in the production of durable, heat-resistant dinnerware. Melamine is formed by polymerizing melamine with formaldehyde.
- Properties: Melamine resins offer high resistance to heat, moisture, and chemicals. They also have tremendous electrical insulating properties and are used in applications requiring flame resistance.
- Applications: Melamine resins are used in electrical insulators, laminates (e.g., Lamitex NEMA Grade G9), and decorative surfaces like kitchen countertops.
Polyester Resins:
- History: Polyester resins were first introduced in the 1930s and became popular in the 1940s for their versatility and ease of use in composite manufacturing.
- Properties: Polyester resins are known for their good mechanical properties, chemical resistance, and ease of processing. They are often used in combination with fiberglass reinforcements.
- Applications: Common applications include boat hulls, automotive panels, and electrical components like NEMA Grade GPO-3.
Common Reinforcements of Thermosetting Resins
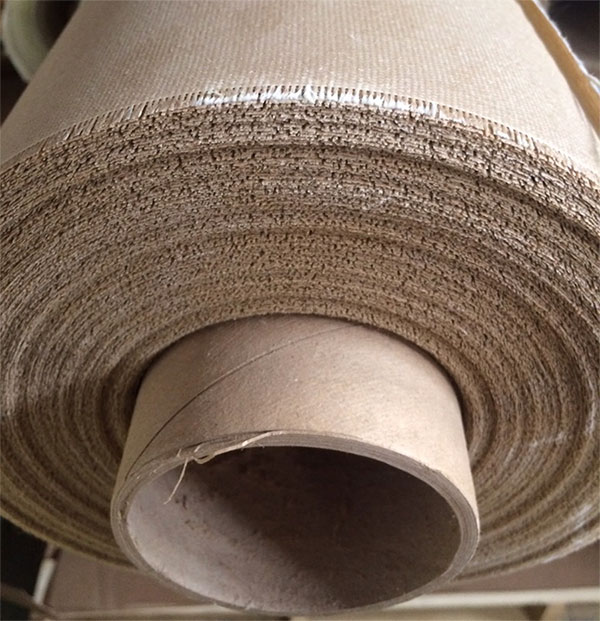
Glass Fibers:
- Properties: Glass fibers significantly increase the strength, stiffness, and dimensional stability of the composite. Well known for having low moisture absorption characteristics, they also enhance the thermal and electrical insulating properties.
- Applications: Glass-reinforced thermosets are used in a wide range of applications, including printed circuit boards, structural components, cryogenic and electrical insulation.
Paper:
- Properties: Paper is used as a reinforcement in phenolic laminates to provide good electrical insulation and moderate mechanical strength. Paper-reinforced thermosets are lightweight and have good machinability.
- Applications: Paper-reinforced phenolic laminates, such as Lamitex NEMA Grade XX, are commonly used in electrical insulation, terminal boards, and relay bases.
Cotton Fabric:
- Properties: Cotton fabric reinforcement provides excellent impact resistance, machinability, and dimensional stability. These composites have good electrical insulating properties and are resistant to moisture and chemicals.
- Applications: Cotton-reinforced phenolic laminates, such as Lamitex NEMA Grade CE, are used in gears, pulleys, and electrical components requiring high impact strength and wear resistance.
Where are they typically used?
Aerospace: High-strength, lightweight composites are used in aircraft components, such as wings, fuselage sections, interior panels, shims, and rocket motor casings.
Automotive: Thermoset composites are used in body panels, engine components, and electrical systems for their durability, heat resistance, and insulating properties.
Electrical Distribution and Electronics: Thermosetting resins are essential in printed circuit boards, low-dissipation panel boards for De-energized and on-load tap changers, electrical insulators, and switchgear due to their excellent electrical insulating properties.
Construction: Thermoset composites are used in building materials, including countertops, wall panels, and roofing materials, for their durability and resistance to moisture and chemicals.
Oil & Gas: Thermosets are used in a wide range of applications in the Oil & Gas industry. Everything from seals, gaskets, pumps, plugs and gauges are typically made with these materials.
Thermoset composites represent a crucial class of materials that combine the strength, stability, and insulating properties of thermosetting resins with the enhanced mechanical properties provided by various reinforcements. From their early use in Bakelite products to their modern applications, thermoset composites continue to play a vital role in the advancement of technology and industry.