Detecting and Understanding Circumferential Hairline Cracking in Composite Tubes
Composite materials, with their high strength-to-weight ratio and versatility, are widely used in various industries. However, like any material, composites are susceptible to defects that have the potential to compromise their performance. One such defect is circumferential hairline cracking in composite tubes. In this technical blog, we explore the causes, detection methods, and mainly, the differences between circumferential cracking and another common defect—delamination.
1. Circumferential Hairline Cracking
What Is It?
Circumferential hairline cracking refers to small, fine cracks that encircle the circumference of a composite tube. These cracks are typically shallow and run parallel to the tube’s outer surface. Picture below: an example of a tube with an extreme amount of circumferential cracking. Hairline cracking, unless extreme, has not been shown to cause a dramatic effect on the overall mechanical properties and bond strength of the tube. As they are inside the wall thickness of the tube, they often go unnoticed.
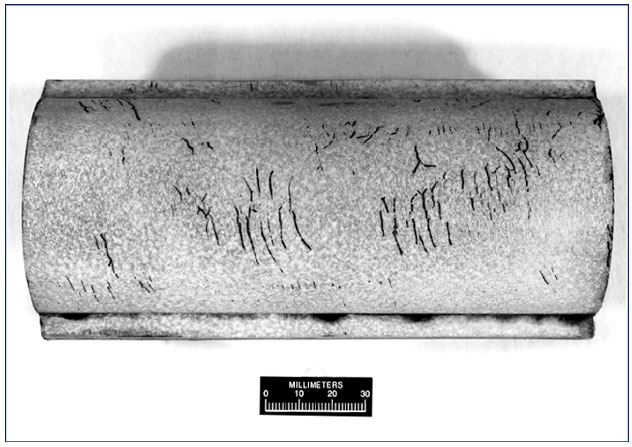
Causes
- Fiber Misalignments: Improper alignment of fibers during manufacturing creates localized stress concentrations.
- Voids or Inclusions: Air pockets or foreign particles disrupt material continuity.
- Residual Stresses: Uneven curing or cooling leads to residual stresses.
- Improper Curing Conditions: Incorrect temperature, pressure, or curing time.
Detection Methods
- Eddy Current Testing (ECT):
Efficient for small-diameter tubes.
Detects both axial and circumferential cracks.
- Pulsed Magnetic Flux Leakage (MFL):
Non-contact method for examining pipelines.
Detects circumferential defects.
- Surface Inspection with Eddy Currents:
Pass ECT probe over the tube surface.
Effective for hairline cracks.
2. Delamination
What Is It?
Delamination involves the separation of layers within a laminated composite material. It appears as distinct layers peeling apart, creating voids or gaps between adjacent plies. This can be a serious issue with the mechanical, electrical, and thermal properties of the tube itself.
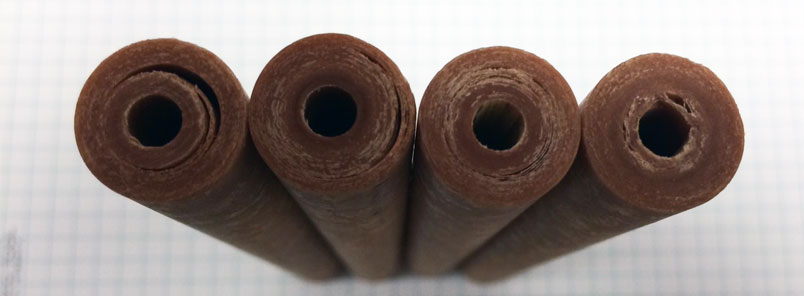
Causes
- Poor Adhesion: Inadequate bonding between layers during layup due to lack of resin (‘dry prepreg’), or the bond strength of the resin itself.
- Impact or Stress: External forces cause layers to separate. Example: when pulling the winding mandrel out of the tube after curing (as shown I the picture above)
- Manufacturing Defects: Uneven curing (resin impregnation / heat of oven), improper tooling, or surface imperfections.
Detection Methods
- Ultrasonic Testing (UT):
Common for detecting delamination.
Sends ultrasonic waves through the material.
Measures reflected waves to identify voids.
- Thermography:
Detects variations in heat flow caused by delamination.
Requires thermal imaging equipment.
- Visual Inspection and Tap Testing:
Visually inspect the surface for visible delamination.
Tap the material and listen for changes in sound.
Understanding these defects is crucial for maintaining safe and reliable composite structures. Whether you’re designing cryogenic components, electrical insulation, aircraft components, wind turbine blades, or sporting equipment, vigilance in defect detection ensures the longevity and performance of composite materials.
1. Reference for picture of circumferential hairline cracking: Why Do Kraft Recovery Boiler Composite Floor Tubes Crack? - Scientific Figure on ResearchGate. Available from: https://www.researchgate.net/figure/Circumferential-cracks-are-found-on-some-tubes-indicating-the-tensile-stresses-on-the_fig5_298084392 [accessed 28 Dec, 2023]